Estireno Acrilonitrila(SAN)
O Estireno Acrilonitrila pode ser produzido através de três métodos industriais diferentes que são: processo por emulsão, processo por suspensão ou pelo processo de alimentação contínua.
Comparação entre os três processos:
O processo por emulsão e por suspensão é aplicado na produção de componentes moldáveis ou para a preparação do SAN na mistura de outros monômeros para a fabrição de outros polímeros como por exemplo o polímero ABS(Acrilinitrila Butadieno Estireno).
O método que gera menos gasto de água e outros químicos intermediários na reação e que causa um menor impacto ambiental é o processo de alimentação continua. Por não conter resíduos de emulsificantes ou agentes suspensores, normalmente, o SAN produzido por esse método atingem uma coloração melhor apresentam maior facilidade de de moldar e esse tipo de SAN é preferido em aplicações em que são exigidas um maior grau de transparência óptica.
O processo de alimentação continua é mais econômico por ter menor gasto de energia por causa da ausência da etapa de secagem, por apresentar uma maior eficiência na utilização do tempo e espaço da planta industrial, além de gastar menos água e outros químicos como citado anteriormente.
Uma das desvantagens dessa forma de fabricação é a alta viscosidade apresentada pelo estireno acrilonitrila dentro dos reatores, que exige uma agitação e dissipação do calor eficientes, tornando muito difícil a elaboração correta dos equipamentos.Um outro problema é que por ser um processo continuo, são gerados produtos não desejados até que o regime transiente acabe.

Fluxograma citado no livro Encyclopedia of Chemical Technology Volume 1 (Kirk-othmer)
O processo:
1)O estireno e a acrilonitrila são postos dentro do reator que manterá uma temperatura de 150°C para que ocorra a conversão de aproximadamente 73% dentro de 55 minutos.Nessa etapa, o calor gerado durante a polimerização é removido pelo contato dos reagentes com a parede resfriada do reator.
Obs1: Nesse caso a conversão de apenas 73% foi feita para facilitar o bombeamento da mistura de polímero formado e o excesso dos reagentes dentro dos tubos até o devolatilizador. Em alguns casos, o fabricante também pode optar por ter uma taxa de conversão acima dessa porcentagem e utilizar um solvente para diminuir a viscosidade da mistura e assim, facilitar o seu bombeamento.
2)Após a reação ocorrer, o polímero fundido de alta viscosidade sai do reator e entra no devolatizador , que serve para retirar os componetes mais voláteis dentro da mistura. Através do uso da baixa pressão (4 kPa ou 30 mmHg) e alta temperatura (220°C), esse equipamento retira os monômeros e outros reagentes em excesso. O produto final deverá ter uma porcentagem de substâncias voláteis menores do que 0,7% em sua composição.
Obs2: Dependendo do caso, pode se utilizar dois devolatizadores em série. Nesse caso, a qualidade final do produto será maior e ficará mais fácil de controlar o processo se comparado à utilização de um único devolatilizador.
3)O produto final é resfriado para que se torne sólido e moído em grãos para facilitar a venda e distribuição para as outras indústrias.
Diagrama de blocos simplificado:
Hipóteses
H1: A produção anual é de 50.000 toneladas.
H2: A fábrica não apresenta vazamentos e seu funcionamento é ininterrupto.
H3: o produto final é considerado puro.
H4: A conversão de polimerização é de 73%.
H5: Usualmente, a proporção de monômeros varia de 20/80% a 30/70%.Para efeitos de simplificação dos cálculos, a proporção adotada será de três partes de estireno para cada parte de acrilonitrila.
H6: Aproximadamente 10% da corrente é composta por solventes e aditivos.

Balanço de massa

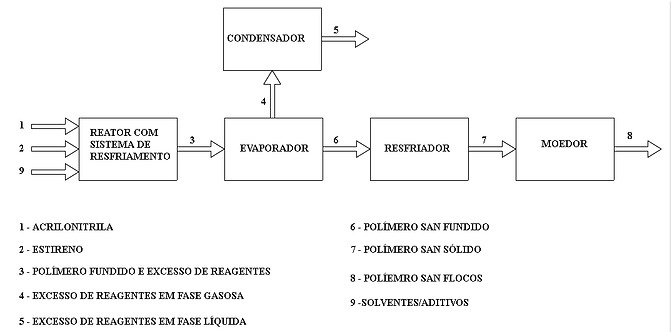